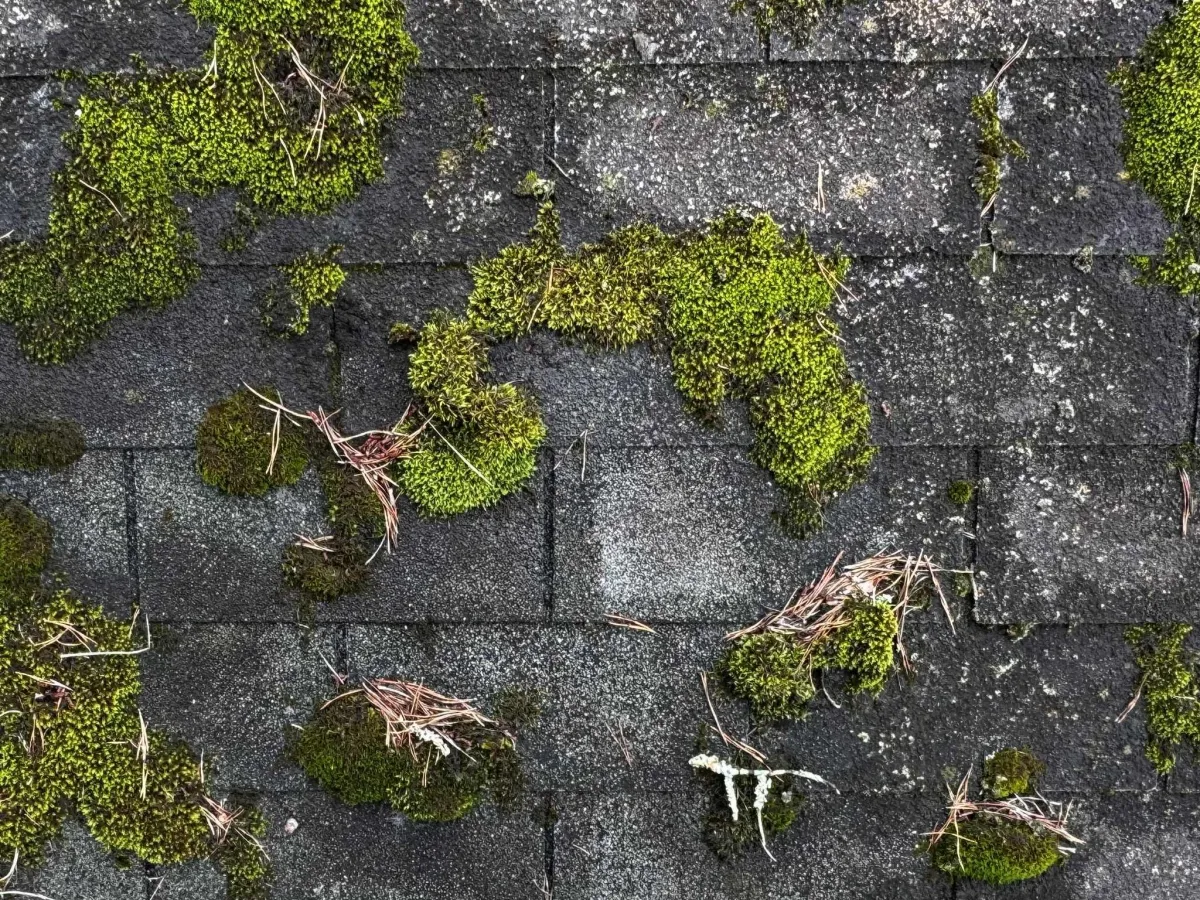
9 Reasons Your Asphalt Shingle Roof Might Not Last As Long As It Should
Asphalt shingle roofs, when correctly installed, typically offer reliable protection for decades. However, premature failures are unfortunately common due to specific, preventable factors. This comprehensive analysis examines the leading causes behind these early failures, providing roofing professionals actionable insights to enhance their practices and deliver enduring installations.
9. Improperly Installed Underlayment
Roofing underlayment acts as an essential secondary moisture barrier beneath shingles. Improper installation—such as inadequate overlap, wrinkles, gaps, or incorrect fastening—allows moisture infiltration, resulting in decking damage and premature shingle deterioration. Inadequate underlayment can rapidly escalate minor issues into extensive roof failures.
These mistakes frequently result from insufficient training, hurried installations, or negligence. Roofing professionals should adhere strictly to established underlayment installation guidelines, ensuring correct overlaps, adequate fastening, and a smooth surface. Incorporating rigorous installation standards, crew training, and frequent quality inspections greatly reduces the likelihood of these preventable failures.
8. Manufacturer Defects
Although relatively uncommon, manufacturing defects represent a notable cause of premature asphalt shingle failures. Common defects include inconsistent granule adhesion, faulty sealing strips, inadequate asphalt saturation, and compromised dimensional stability. These defects accelerate aging processes, reduce waterproofing effectiveness, and undermine overall roof performance.
When suspected, defects often go unreported due to inadequate understanding of warranty procedures or insufficient documentation practices. Roofing professionals must thoroughly inspect new shingles upon delivery and installation, carefully documenting anomalies and promptly addressing any concerns with manufacturers. Adopting detailed record-keeping protocols and clear communication strategies facilitates efficient warranty claims and maintains customer trust.
7. Using Incorrect Products on Low-Slope Roof Sections
Low-slope roof sections necessitate specialized roofing products designed for prolonged water exposure due to slower drainage. Asphalt shingles installed on slopes below manufacturers' minimum recommended pitches inevitably accumulate standing water, leading to accelerated deterioration, leaks, curling, and blistering.
This mistake typically occurs from a misunderstanding of product specifications or attempts to simplify installations by using uniform materials. Roofing professionals must closely follow product guidelines and opt for appropriate alternatives such as modified bitumen, self-adhering membranes, or EPDM rubber roofing on low-slope sections. Comprehensive training and clear communication of product specifications prevent incorrect installations and significantly enhance long-term performance.
6. Reusing Damaged Flashings
Flashings are integral components designed to waterproof transitions, valleys, and penetrations in roofing systems. Reusing flashings that have prior nail holes, corrosion, or physical deformities severely compromises roof integrity. These vulnerabilities allow water intrusion, accelerating deck degradation and leading to rapid shingle deterioration. Improperly sealed flashings can become a primary source of chronic leaks, driving costly callbacks and repairs.
Reuse of flashings typically results from cost-cutting measures or inexperienced roofing teams unaware of industry best practices. Proper roofing practice demands replacing all flashings during roof replacements. Professionals should always inspect and install new, high-quality flashings tailored specifically for each project. Adopting clear installation standards and providing ongoing crew training significantly reduces the likelihood of this common oversight.
5. Improper Nail Placement and Wind Vulnerability
Incorrect nail placement remains a significant contributor to premature shingle roof failures. Nails placed too high, too low, or at improper angles on the shingle strip severely reduce holding power, leaving shingles vulnerable to wind uplift and tear-offs. High nailing, in particular, allows shingles to lift easily, facilitating moisture penetration and rapid degradation of roof integrity.
This problem often arises due to rushed installations, inadequate training, or oversight. Roofing contractors must rigorously adhere to manufacturers' explicit nail placement guidelines, typically detailed within the shingle nailing zone. Providing continuous training and implementing regular quality assurance inspections during installations can effectively mitigate this risk, greatly improving roof durability and resilience against strong winds.
4. Accelerated Degranulation Due to Hail Damage
Hailstorms commonly lead to accelerated granule loss, exposing underlying shingle materials to damaging UV radiation and weather elements. Rapid degranulation drastically shortens the lifespan of shingles, causing them to become brittle, curl, and crack prematurely. Without timely intervention, hail-damaged roofs quickly lose their protective capabilities, resulting in costly interior damage and structural complications.
Accelerated granulation often goes unnoticed due to insufficient post-storm inspections or a lack of trained personnel capable of identifying subtle damage signs. Roofing professionals should perform thorough evaluations after hail events using established industry guidelines. Documenting evidence meticulously and educating clients about the long-term risks associated with untreated hail damage ensures timely insurance claims and necessary roof restorations.
3. Poor Attic Ventilation and Heat Accumulation
Inadequate attic ventilation traps excess moisture and heat, severely impacting shingle lifespan. Elevated attic temperatures accelerate shingle aging, granule loss, and brittleness, while trapped moisture promotes mold growth, wood rot, and decking delamination. Chronic ventilation issues directly contribute to extensive structural deterioration and premature roof failure.
These problems typically stem from improper design, inadequate ventilation system installation, or blocked vents. Roofing contractors must design and implement effective ventilation solutions, such as ridge and soffit vents, combined with mechanical ventilation when necessary. Regular inspections and homeowner education on attic ventilation importance help maintain optimal conditions, prolonging roof longevity.
2. Improper Installation and Use of Short-Lived Products for Flashings
Using inappropriate or short-lived flashing products, particularly at penetrations and intersections, significantly increases premature roof failures. Cheap, thin aluminum flashings, inappropriate caulking, or inadequate sealing materials deteriorate rapidly, allowing water intrusion and subsequent damage.
Contractors may opt for inferior materials to reduce initial costs or due to inadequate knowledge of material longevity and compatibility. Roofing professionals should specify and install robust, corrosion-resistant flashings such as heavy-gauge aluminum, galvanized steel, or copper, depending on project requirements and local environmental factors. Providing detailed material guidelines and ongoing professional training ensures lasting installations and superior waterproofing performance.
1. Installing Over Delaminated or Rotted Decking
A critical yet frequently overlooked aspect of shingle roofing is the condition of the roof decking. Decking forms the foundational surface for shingles, and its integrity is paramount for a roof's overall performance. Installing new shingles over compromised decking, such as delaminated plywood, rotted wood, or weakened OSB panels, drastically reduces roof lifespan. Poor decking undermines nail retention, decreases wind uplift resistance, and exacerbates moisture penetration problems. The compromised structural integrity can also lead to sagging and ponding, further increasing vulnerability to water infiltration and damage.
This mistake commonly occurs due to inadequate inspection procedures or attempts to cut costs by bypassing decking replacements. Contractors may mistakenly believe minor surface damage poses no significant risk or might rush projects to meet tight deadlines. To prevent this, thorough inspections should always be conducted before installation. Damaged decking must be fully replaced or repaired according to industry standards and local building codes. Proper training and adherence to standard procedures ensure long-term performance and customer satisfaction.